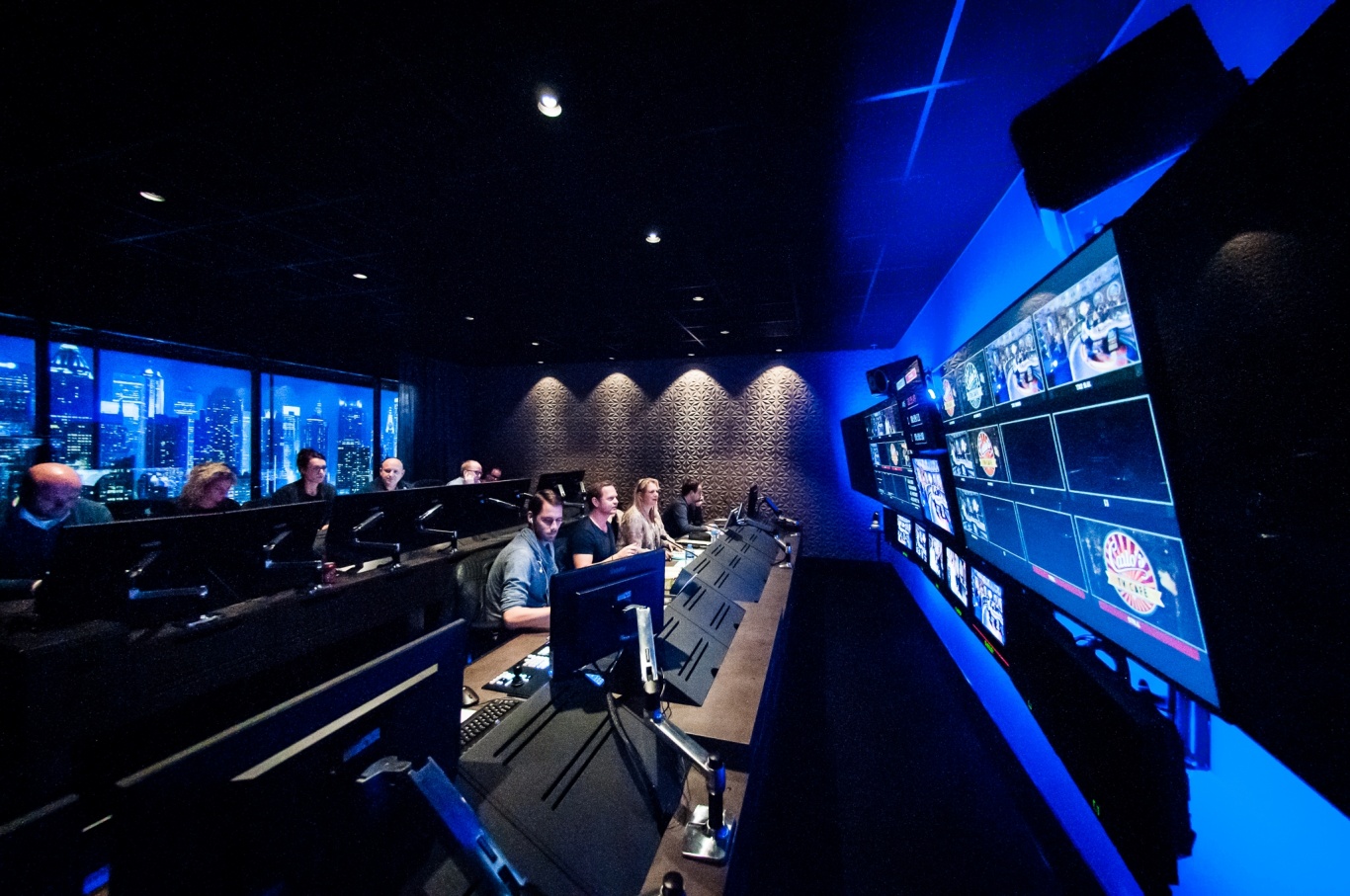
NEP’s market-leading centralised production model – and an IBC exclusive
Earlier this year, we wrote about centralised production and how it’s increasingly deployed to utilise spare capacity of the production team, technology and equipment on additional productions, simultaneously.
In that post, we looked at global outsourced production company NEP, who are leading the way in centralised production, which is now a core product for the business.
Frame 25 spoke to Casper Choffat, a Netherlands-based media solutions director at NEP, who leads a team of 14 people focused on creating end-to-end solutions based on customer requests or internal needs.
We asked Casper exactly how – and why – NEP are engaged in centralised production, what drawbacks they’ve faced and how they see things evolving in the future.
Frame 25 (F25): Tell us about the logistics involved in your centralised production operation.
Casper Choffat (CC): We focus on a centralised model, where all the kit needed for a production is housed in a datacentre and connectivity goes into the venue to connect cameras and microphones back into the datacentre. And we have production, shading and sound control elsewhere, also connected to the datacentre.
We work across centralised equipment as much as we can inside the datacentre, and only have what we need specifically in the venue or in the control room, as required.
F25: How long have you been using this model?
CC: We’ve been producing content in this way since 2015, and in that time we’ve used it to make approximately 5,000 productions – and that’s just in the Netherlands.
The model that we built there has also been ported into Australia, where we’re doing this on a larger scale.
We’ve built the same model and two hubs – in Sydney and in Melbourne – which are connected to rugby and football stadiums in Australia, and the production crew sits in either of those cities, depending on the sport, and the camera crew and some engineers are at the venue in order to connect all that kit back into the hub.
We don’t have to go through the Netherlands. We just took the same model and made it larger. The longest distance is 4,500km – from Perth to Sydney.
F25: Why Australia?
CC: It’s a combination – that market is very strong for these types of productions. As well the 4,500km between Perth and Sydney, we also have venues that are 1,000km away from Sydney and Melbourne, where most of the production talent actually live and work, so they’d need to travel quite a bit to get to those different locations, and that doesn’t necessarily increase the quality of the production.
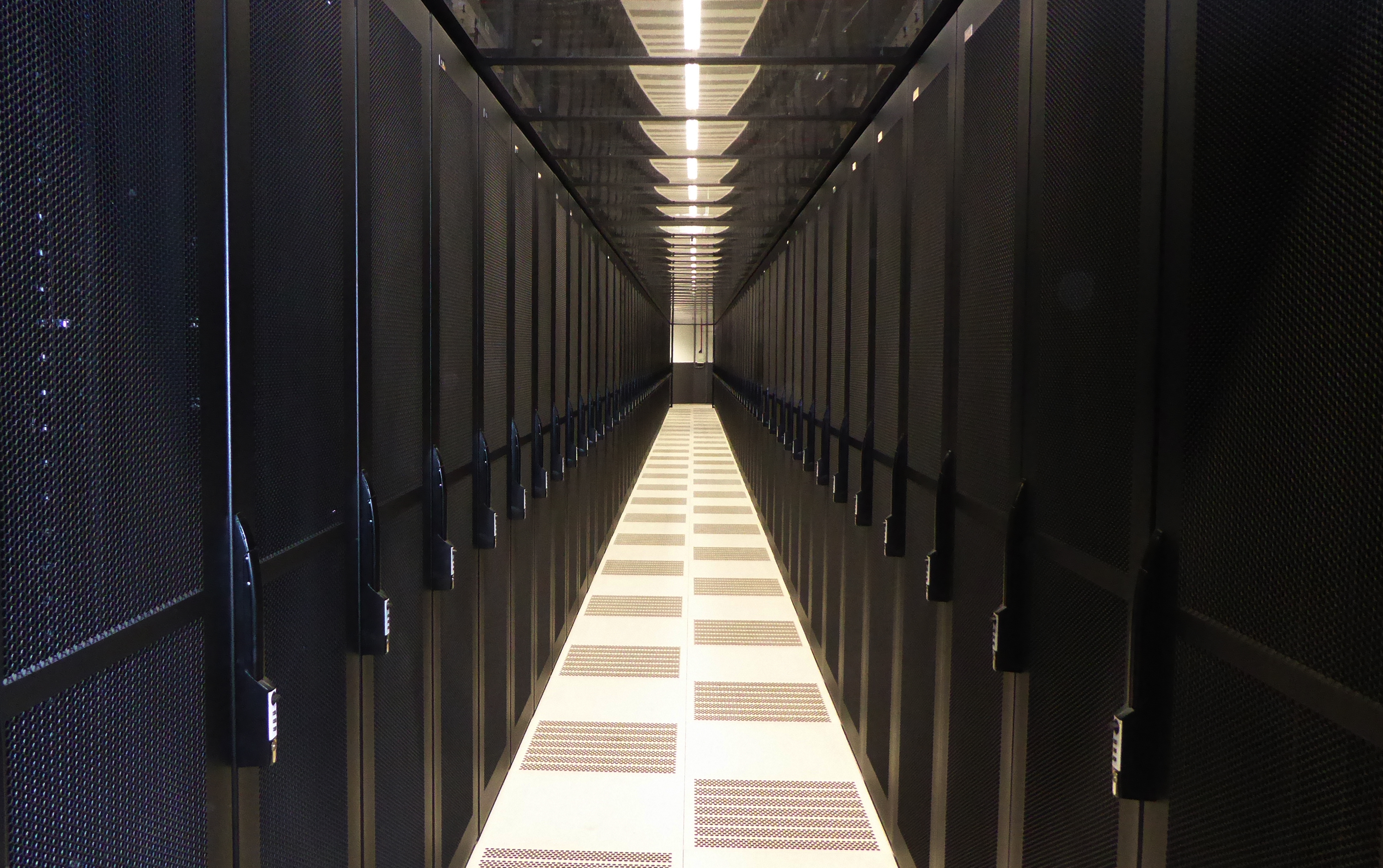
F25: What are the biggest advantages of centralised production?
CC: More consistency and efficiency, higher quality and better work/life balance. And it’s environmentally friendly.
Production crew don’t have to travel as much as they would have when they’re not working with this model, so they can be with their families, they can just drive to a nice office, have nice coffee and have nice lunch, instead of running around for the production without all the necessary facilities at the same quality-level.
There are also cost savings, because of the workforce’s reduced travel. Beyond that, there are environmental benefits to be had as fewer people are getting on a plane to work on-site thousands of kilometres away from a production base.
F25: Latency has been the biggest hurdle to overcome. Is that still the case?
F25: What about other drawbacks?
CC: You need the connectivity and that can be expensive. It all depends on whether a telco really has connectivity into a venue, and if that’s strategically situated for our datacentre. That’s one drawback.
Another that I see, particularly when we started to use this model, was a big pushback from the people who actually do the productions because they wanted to be on-site. Some people like the feeling of working away from home, they like to be away from home rather than in the office.
But what we’ve found after doing this for quite a while is that people actually started liking it more. There was a fear of the unknown.
To respond to that pushback from the production team, we started developing something that we will launch at IBC, so make sure you visit our booth (located in Hall 14, booth H.02).
We can have a production crew working on-site but still within a model that is central.
F25: Sport, by its nature, suits centralised production but what about other genres – news, for example?
CC: For sure. Sport is a natural fit, as we’ve been showing in Australia, but in the Netherlands we use this model for entertainment and talk shows as well, not just sports.
I definitely also see a possibility for news – basically, anything that we can get connectivity into, where we can do a lot of shows one after another. So sports, obviously, but also more ‘repeatable’ work is suited to this type of model.
F25: What competition does NEP face in the remote production space?
CC: As a business, we see competition in different forms. But in this model, we do see competition in centralised production, and we’re seeing more businesses using it. But in our model, we don’t see a lot of vendors or service providers doing that the way we are doing it today.
That’s not only in the production space but also in the post-production space that we do that.
Sure, we have competition because ultimately, for some companies, it’s about price, but we offer a significant competitive advantage with an eye on the future.
F25: Speaking of the future, how do you see the model or centralised production evolving?
CC: What we’ve seen over time is that connectivity – and the equipment that you need to have connectivity – drops in price.
To deliver broadcast through a centralised model, you need bandwidth. That’s the biggest challenge. In order to get bandwidth, you need kit that provides that bandwidth, and if that kit is very expensive then probably the figures don’t make sense to use a centralised model.
As new kit with higher bandwidth is released, the equipment that it replaces – which still handles the required bandwidth – reduces in price.
We’ll see more and more of this model, moving forward.
The NEP booth at IBC is located in Hall 14, booth H.02. IBC is held at the RAI, Amsterdam, and the 2019 edition runs from 13-17 September.
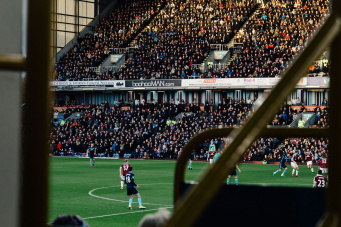
Product + audience + platform: why the Premier League is going its own way
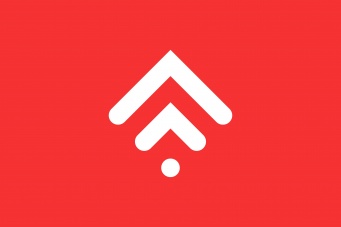
In The Frame - April '23
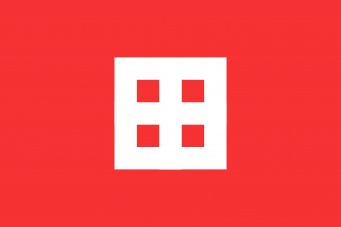